
86 17344894490
service@chalcoaluminum.com
- Alüminyum alaşımlı kurban anot
- Magnezyum alaşımlı kurban anot
- Etkilenen mevcut katodik koruma serisi
Araç imalatında ekstrüde alüminyum profil yapısal parçaları
Bilgilere göre, Avrupalı lokomotif ve araç üreticilerinin mevcut siparişlerinin yaklaşık% 60'ı alüminyum gövdeli araçlardır. 20 yıl önce, bu tür siparişler sadece% 2 -% 3 idi. Artık alüminyum yapı buz, tgv-2n, etr460, etr500, Talgo Hotel tren ve diğer yüksek hızlı trenlerin yanı sıra birçok banliyö ve şehir içi demiryolu ulaşım aracında da uygulanmaktadır.
Ekstrüde alüminyum profil yapısal parçalarının benimsenmesi 1970'lerin başında başladı. O zamanlar, alüminyum profillerin uygulanmasındaki bilimsel ve teknolojik ilerleme, alüminyum bileşenlerin istenen şekil ve boyuta göre yapılmasını mümkün kılmıştı. Bu alüminyum bileşen, İngiltere'deki apt trenlerinin eğimli araba gövdesine uygulanmıştır. Bununla birlikte, o zamanlar, ekstrüde alüminyum bileşenlerin uygulanması büyük faydalar sağlamadı, yani daha yüksek malzeme fiyatları, imalat iş yükünün azaltılması için telafi edilmedi. O zamanlar, büyük boyutlu yapısal parçaların kullanılması, otomobil gövdesinin üretim iş yükünü sadece% 40 oranında azalttı ve 26m uzunluğundaki otomobil gövdesinin ölü ağırlığını 7.5t'ye düşürürken, 26m uzunluğundaki çelik otomobil gövdesinin ölü ağırlığı 11T idi. 1970'lerde, demiryolu departmanı, araçların tüm hizmet ömrünün toplam maliyetinin hesaplanmasına daha fazla dikkat etti (satın alma maliyeti artı işletme ve bakım maliyeti). Tren çekiş enerjisi tüketiminin, büyük ölçüde demiryolu araçlarının kendi ağırlığına bağlı olan aynı seviyede tutulması gerektiğini fark ettiler.
Daha sonra, enine sabitleme ihtiyacını en aza indirgeyen, çift katmanlı kabuğun büyük boyutlu yapısal parçalarının ekstrüzyon yönteminin benimsenmesi gibi, en önemlisi 1980'lerin ortalarında elde edilen bazı yeni teknik ve teknolojik önlemler, araç alüminyum gövdesinin üretim süresini daha da azalttı, çelik araçlara kıyasla% 50 oranında azaldı, ve geleneksel yönteme göre çift katmanlı silindir gövdesi yapmak mümkün olmuştur ve daha sonra pencere deliklerinin açılması Kaynak işlemlerinin tümü, yalnızca kısmen robot teknolojisi ve ekipmanı kullanılarak, birleşik teknik işlemler sürecinde tamamlanmaktadır.
Şimdi, demiryolu departmanları yeni araçların geliştirilmesine katılımlarını kademeli olarak ve daha fazla azalttığında ve ilk üretim maliyetlerini ve gelecekteki işletme giderlerini azaltmak için satın alma politikaları uyguladığında, üreticiler abonelerin teknik gereksinimlerini karşılamak ve pazarın gelişme eğilimine uyum sağlamak için yeni yapılar ve malzemeler benimseme konusunda daha fazla özgürlüğe sahipler. Ekstrüde alüminyum profil yapısal parçaları , araç yapısı için bazı katı gereklilikleri karşılamada başka avantajlara da sahiptir. Örneğin, çift katmanlı kabuk ekstrüzyon yapısının sertliği, yüksek hızlı tren buluştuğunda üretilen aerodinamik etkinin özel darbe dayanımına sahip olmasını sağlayabilir. Bu yapıya sahip otomobil gövdesinin bir diğer önemli özelliği de büyük uzunlamasına sertliğidir. Uzunlamasına ve enine sertlik oranı 70:30'a ulaşabilirken, çelik otomobil gövdesinin oranı 40:60'tır. Ek olarak, alüminyum profiller, dolgu maddeleri ve çok fazla manuel çalışma gerektirmeden, iyi dış şekil gereksinimlerini de karşılayabilir. Örneğin, Alman Federal Demiryolu'nun bazı modelleri için, dolgu maddesi kullanılmadığından, hesaplamadan sonra, boya kaplaması ile birlikte, öz ağırlık 500kg olabilir.
Ekstrüde alüminyum profil yapısal parçalarının kullanımı da araç üreticilerini karmaşık görevlerle karşı karşıya bırakmaktadır. İşgücü ve malzeme fiyatları arasında bir denge bulmalı ve tasarımcıların bu dengeyi sağlamak için çaba göstermelerini sağlamalıdırlar. Malzemenin tüm kavramda sadece bir faktör olduğu açıklığa kavuşturulmalıdır. Benimsenen üretim süreci ve teknik süreç de işletmenin üretim kapasitesine uygun hale getirmek ve yatırımla dengelenmesini sağlamak için ayrıntılı olarak formüle edilmelidir.
Örneğin, çoğu makine imalat şirketi için, üretim araçlarının rezervlerini en aza indirmek en önemli önceliktir. Tasarımcıların malzeme ve süreç seçimi bu konuda önemli bir etkiye sahiptir. ABB, her hafta alüminyum gövdeli 8 araç üretebilen bir üretim hattına sahiptir ve bu da toplam malzeme depolama maliyetini% 8 oranında azaltır. Ancak malzeme kullanımından kaynaklanan teknik süreçteki değişiklikler nedeniyle bu denge kolayca bozulur. Örneğin, kaynaktan yapıştırmaya geçiş, yapıştırma sertleştirmesi için gereken önemli süreyi telafi etmek için daha fazla günlük rezerv gerektirdiğinde.
Demiryolu taşıtları üretimi için alüminyum profillerin bir diğer lider tedarikçisi Almanya'nın VAW şirketidir. Şirketin liderleri, araç yapısının standardizasyonunda ve modül tasarım yönteminin benimsenmesinde büyük bir gelişme eğilimi olduğunu öngörmektedir (bu eğilim pazar talebi nedeniyle güçlendirilmiştir, bu nedenle üreticilerin desteğine sahiptir) ve Almanya'da yerel demiryolu taşımacılığının bölgeselleştirilmesi için pazar talebini göz önünde bulundurarak, Bazı özel şirketler, bireysel sipariş verenlerin gereksinimlerini daha büyük ölçüde karşılamak için standartlaştırılmış modül yapısını kullanmaya daha fazla dikkat edecektir. Şu anda, çeşitli Avrupalı lokomotif ve araç üreticilerinin çok sayıda tasarım fikri vardır ve bu fikirler modül tasarımına dayanmaktadır. Standardizasyon ve modülerliğe yönelik bu dönüşüm hem üreticiler hem de kullanıcılar için faydalıdır. Araç imalatında alüminyum profil kullanımının genişlemesi, otomatik kaynağın daha geniş kullanımı nedeniyle üretim döngüsünü büyük ölçüde azaltacaktır.
Kaynaklı alüminyum gövdeli araçların, sürüş güvenliğini artırmaya elverişli olan yüksek darbe yükü direncine sahip olduğu da açıktır. ABB, alüminyum yapının yıkım testini organize etmek ve gerçekleştirmek için 1 milyon lira yatırım yaptı ve beklenen test sonuçlarını tatmin edici ve daha da önemlisi elde etti. Şirket ayrıca kaza yapan araçların arıza yöntemlerinin onarımında değerli pratik deneyimler biriktirmiştir. 1994 yılının başında, Fransa'da GEC Alstom tarafından sipariş edilen tgv-2n treninin çift katlı binek otomobil test numunesi üzerindeki hasar testi, darbe kuvveti 250t olduğunda, 8mj'nin emilen darbe enerjisi nedeniyle, yapının toplam 80 cm boyunca ekstrüde edildiğini ve alüminyum gövdenin bir bütün olarak bozulmadan kaldığını kanıtladı.
Aynı zamanda, alüminyum otomobil gövdesinin avantajlarının tanınması sorunsuz değildir. Çelik gövdeli lokomotif ve araç üreticileri, Almanya'daki buz trenlerinin üretim sürecinde alüminyuma yapılan vurgu konusundaki endişelerini dile getirdi ve 1994 yılında çeliğin üstünlüğünü doğrulamak için bir çalışma yürüttü. Bununla birlikte, daha önce olduğu gibi, çelik yapının kullanımı, otomobil gövdesinin ölü ağırlığında yaklaşık% 20'lik bir artışa yol açmaktadır.
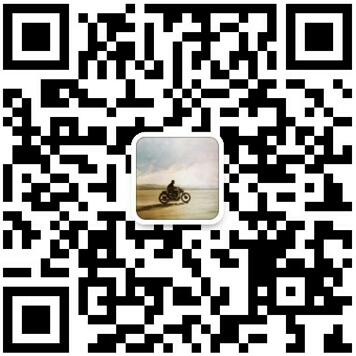
Ücretsiz ürün teklifi, herhangi bir zamanda danışmak için hoş geldiniz, ilk cevabı vereceğiz. E-postamız: